E-commerce logistics: How to receive goods

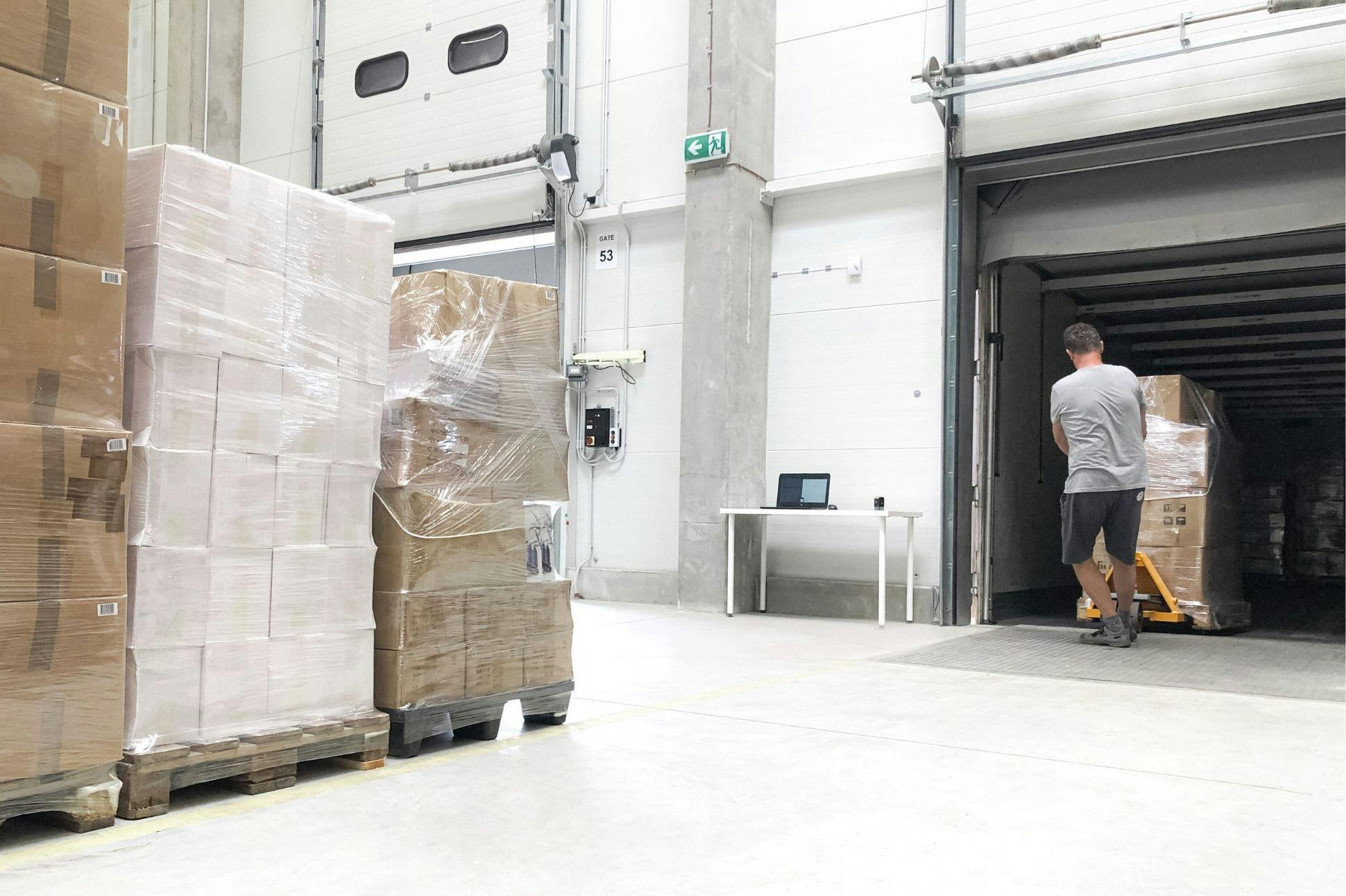
Receiving goods may seem like a simple process. You order the goods from your supplier, receive them at your warehouse gate and then put them on the shelves. Yes, in a nutshell, that is indeed the case. But receiving needs to be looked at in a more complex and detailed way because its quality affects the efficiency of next steps in the supply chain such as inventory management, picking, packing and shipping. The more your business grows the more important it will be to get the process right. In fact, it’s not just the overview of stock that significantly reduces operating costs.
In the article you will gradually learn which steps the goods reception consists of, what are our recommendations for optimization and what benefits result from its correct setup.
What is receiving goods
Receiving of the goods is the first step of the fulfillment process. It involves delivering the goods to the warehouse, unloading, checking and storing them in the warehouse for future customer orders.
Goods receiving – step by step
The ideal result of receiving is to place the SKUs in the correct positions and in the required quantity. “Placing in the correct positions” means stocking and sequentially adding identical products in the smallest possible warehouse space and according to how often a particular product is ordered.
E-commerce businesses should have a detailed internal manual of the receipt process which includes checklists, Q&A to even less common situations. Ideally, every handling of goods should be recorded and managed by a warehouse management system (WMS). This is even more so as your business grows as this is the only way you will be able to eliminate inaccurate stock levels and other related complications and extra work. So what does the complete receiving process look like?
1. Cooperation with the supplier and sending the goods to the warehouse
The condition for a smooth reception starts with the supplier of the goods. Several rules need to be agreed and followed before they are sent to the warehouse. Based on its demand forecast the online store orders specific numbers of individual products in advance and agrees on their packaging and labelling (ideally so that each piece is marked with its EAN code). The online store can also communicate with the supplier the number and type of handling units (boxes, pallets, etc.), the number of boxes on a pallet, the ideal size and weight of filled boxes, etc.
If the e-commerce business cooperates with an external logistics company (a so-called 3PL), it is necessary to ensure that all conditions for further handling within the supply chain are met.
2. Delivery of goods
The receiving process begins when the goods are delivered to the warehouse. The warehouse staff takes the order at the receiving ramp and unloads the individual pallets / boxes into the designated marked areas. During this handling they visually check the condition of the delivery, or count the number of handling units (pallets and boxes; see below). If the staff notices damaged or missing packaging, they immediately addresses the situation with the driver or their supervisor, who contacts the supplier. In addition, it is advisable to follow two other rules when taking delivery of goods… To allow safe entry and movement of the driver in the designated warehouse area and to have a physical presence of the receiving officer at all times, e.g. in case of a damage incident during unloading.
It is advisable to use appropriate handling equipment for bulky and heavy unloading. If the driver is transporting goods for more than one company, these shipments should be placed in the truck according to the load schedule. This way can warehouse operator unload their cargo without wasting time with other people’s shipments.
The receipt of goods ends with the signing of documents (CMR, delivery note, warehouse receipt, etc.) or electronic approval of the receipt of goods and departure of the driver. In case of incorrect number of received handling units or damage to them, this event must be noted in the relevant document. If the goods are damaged, a damage report shall be filled.
3. Recounting and confirmation of goods received
The next step is to check the delivered goods. Depending on the nature of the goods the online store can decide to process quantity or quality checks.
Quantitative checks can be performed at the level of handling units (boxes, pallets) or products. Checking the number of all products can be time-consuming so some online retailers lean towards the option of randomly checking the contents of selected packages. After the recount it is important to compare the status of the quantity actually received with the quantity ordered. Any discrepancies should be communicated with the responsible party – manufacturer, supplier, etc. These differences should be recorded in the software used for future analysis, e.g. when determining the reliability of individual suppliers in both the quantity and quality of goods delivered.
How it works in Skladon: Our clients have access to the MySkladon application which provides a complete overview of their warehouse management in real time. The app also includes information on individual receipts where they can see the current status of each, the expected number of products from the supplier, the number of products actually counted, the final difference and the number of handling units (see image below).
Occasionally, a situation arises when goods are included in the receipt that were not originally announced. In this case there are two solutions according to the agreement with the client. We accept the goods directly or we “hold them on receipt” and agree with the client on the next steps.
We highly recommend using a warehouse management system (WMS) for quantity checks. Scanning individual items will speed up the process and make it more accurate. The only requirement is that each item is marked with its EAN code. In the case of scanning boxes / pallets they need to be marked with a master label, the form of which is approved and software compatible for all parties involved. Once scanned, the system will register the contents of the specific box / pallet, i.e. the total number of SKUs.
How it works in Skladon: The presence of EAN codes is essential for the accurate management of our clients’ inventories. Every product is scanned at least 4 times during its flow in the warehouse – at receipt, putting into shelve, picking and packing. Further scanning takes place at the point of palletisation but this is done at the order level, not the individual product. Only in this way we are able to ensure a minimal error rate in order handling (in the first quarter of 2021, we reached a level of 0.09%) and achieve the most accurate matching in the inventory of goods.
There is also the possibility of so-called quality checks. Unlike quantity the quality of the product is usually not systemically recognisable. It is therefore important to select specific products and check their quality from production, the condition of fragile goods, etc.
How it works in Skladon: We perform quality checks on several clients, an example is Skinners. The goods are sent to us directly from the manufacturer, so the client does not come into physical contact with their product. We have jointly defined an internal quality manual for the checks, which contains detailed checking instructions.
4. Goods storaging
The final step is to place the new goods in the storage area. This step can vary significantly from warehouse to warehouse. It depends on the type and size of the warehouse or the nature, size, quantity and weight of the received goods. This process is also more efficient in the case of system warehouse management. In practice, it looks like the warehouse staff is offered a storage position after scanning the EAN code of the product. There are usually two reasons for this: either the product is already stored in the position and the addition saves warehouse space or the warehouse position is evaluated as the most suitable according to the turnover rate of the product to be stocked. The second option aims to process incoming orders as quickly as possible.
How it works in Skladon: We stock new goods either on shelves for immediate picking or on pallet positions that serve as a long-term stock (buffer). Some of our clients’ products need to be kitted before they can be stored on the shelves, i.e. we create the final product from the received semi-finished goods. All operations are of course managed and controlled by the warehouse management system (WMS). Furthermore, we do not mix identical products with different batches or expiry dates on individual positions.
How to optimise the receiving process
There are a number of ways to improve the receiving process. Below are some of our recommendations.
Design your warehouse layout correctly
As mentioned earlier, receiving goods is the first step in the fulfillment process. Its location must correspond to the material flow of goods within your warehouse and should meet at least the following 4 basic conditions: continuity with the receiving ramp, sufficient handling space, direct barrier-free connection to all used warehouse positions and separation of the receiving ramp from the dispatch ramp. Proper placement of the receiving area also eliminates crossing routes with handling equipment and personnel from other workplaces.
Cooperate with a warehouse management system (WMS)
The warehouse management system makes it easy to manage your complete supply chain with its features and practical automation. By using it you can refine your warehouse management and achieve greater storage and picking efficiency. You know exactly where and how many products you currently have in stock or how many products are on their way to your warehouse. Among other things you can set up so-called reorder points in the system at the level of individual products. When the selected quantity is reached, you are automatically notified to order new goods at your supplier.
How it works in Skladon: Our clients can track the current status and quantity of their products in their MySkladon account. The application is connected to our WMS with a two-way data flow between the two systems. For each product they have information about the quantity that is:
- Available for future orders
- Reserved in unpacked orders
- Ready to ship
- Held by quality
- On the way to warehouse / ready for stock
This information is also automatically linked to our clients’ online stores so they always have an up-to-date quantity of their products available for new orders.
Check selected goods
If you cooperate with multiple suppliers, time, your own experience and analysis will reveal those who are less responsible in the goods delivering or you will come across so-called problem products (e.g. fragile, with expiry dates, production-specific, etc.). In these cases, be more cautious at the reception as this step is often the last checkpoint. This will prevent claims for damaged, expired, partially missing or differently marked goods.
Documents double checking
Immediately check and compare the ordered quantity with the actual received quantity. This avoids corrections, rework and losses later in the fulfilment process. To streamline your checks, maintain your receipt and shipping record system.
Advantages of a fine-tuned receiving process
Investing in optimizing your receiving process will pay off in all subsequent stages of fulfillment. Properly set up receiving is an important prerequisite for smooth handling of future orders. You can therefore expect:
1. Accurate inventory overview
If you keep accurate stock counts, you are able to better plan orders with your suppliers, reduce unexplained stock-outs or set ideal margin levels in the longer term. You’ll also avoid negative reviews from your customers who have ordered incorrectly kept goods “in stock” from you.
2. Ideal quantity of products in stock
Low inventory levels risk selling out and customers leaving for competitors while excessive inventories of rarely sold products do not bring a return on the purchase cost. Find out the causes of these problems at the beginning.
3. Efficient inventory storage
Optimising the receipt of goods also makes the warehousing process more efficient – both spatially and financially. The goal of every e-commerce business should be to have enough goods in the picking area and as close to the packing area as possible.
Investing in WMS or logistics outsourcing?
As mentioned several times in the article, there are 2 conditions that need to be met for successful receipt of goods. A step by step detailed process and an accurate record of products received.
The products you receive into your warehouse are then (in)shipped to your customers which is reflected in the customer experience and ultimately the success of your business.
If you are at a stage where you are shipping higher hundreds to thousands of orders per month, sooner or later it will be time to purchase a matching WMS. Don’t know what all such a WMS should meet? Download our warehouse management system guide. We have prepared it for you in cooperation with logistics auditor Mr. Rudolf Maly, ALog.
A quality WMS always represents a high upfront investment. In addition, every online business is unique so expect to customize it to your specific requirements which comes with additional costs related to time and energy.
Again, there is a choice. Entrust your logistics to an expert partner who has already fine-tuned their fulfillment service and is ready to help you grow further. Benefit from their expertise and compete with the big e-commerce players with your logistics “at the snap of a finger”.